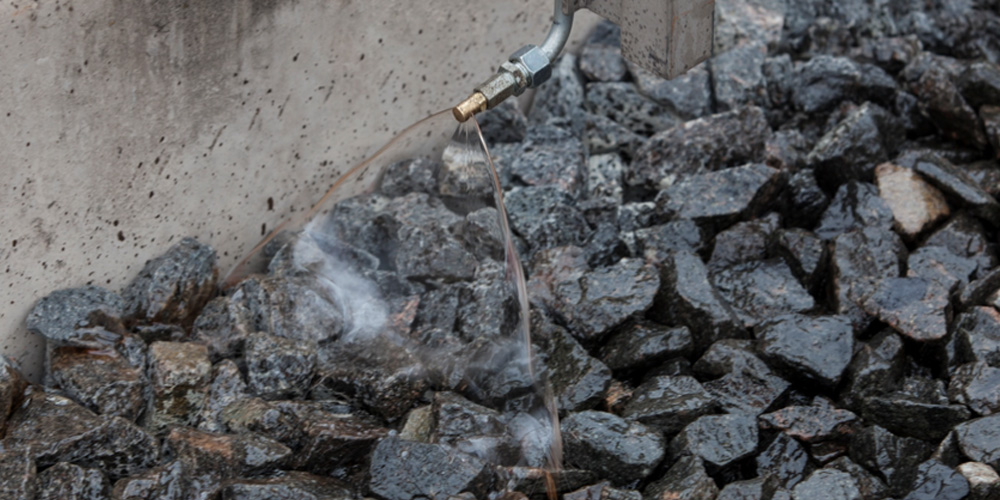
Non-polluting ballast stabilization
Railway tracks today have to meet ever higher requirements with greater track stability and improved travel comfort while at the same time reducing maintenance costs. A decisive factor for success is the ballast bed and our solution for ballast stabilization will help you exploit this. You benefit simultaneously in a number of ways because this single measure enables improvements in a number of different areas.
The ballast stabilization is carried out using mobile two-component mixing devices. This involves use of a hot casting machine, a closed system, which homogenously mixes the special, environmentally-friendly epoxy resin an a curing agent (Amin) to make the end product. Various nozzles then serve to spray it onto the ballast.
Temporary Bonding
When an adjacent track bed on a multi-road track is being improved, the floor level is approximately 1 – 1.5 m below the top edge of the rail. Passing trains and compacting machines may cause the ballast to move, particularly at the sleeper heads, thus affecting the lateral stability of the operational track. This can be prevented by bonding using ® GREBOPOX .
Yours advantages
- lower maintenance costs with longer service intervalls
- low maintenance e.ort, long durability
- sound-absorbing e.ect, e.g. for urban public transport areas
- easy cleaning for ballast surfaces in train stations and stopping places
- approval for use with all large railway
- companies worldwide
- high environmental compatibility, special
- disposal not required
- bonded ballast with full drainage capability
- also easy to work with under extreme weather conditions
- bonded ballast can be reworked, used
- elsewhere, or re-bonded
Ballast Stabilization for points, insulated rail joints and stabilization of deeper levels
Higher cruising speeds and axle loads have increased the demands on railway tracks. Bonding the ballast at insulated rail joints, switches and many other areas stabilizes the track bed, greatly prolonging refill intervals and thus considerably reducing maintenance costs. Bonding the ballast with GREBOPOX® increases ist resistance to lateral movement, as this provides improved stability at greater depths.
Transition areas between ballast track and slab track
Transition areas between ballast tracks and slab tracks are characterized by varying structures and levels of compaction in the track superstructure and base layer, as well as by differences in track modulus values, in addition to any setting processes. Ensuring safety and travel comfort generally requires a high degree of maintenance. Bonding the ballast reduces this need considerably.